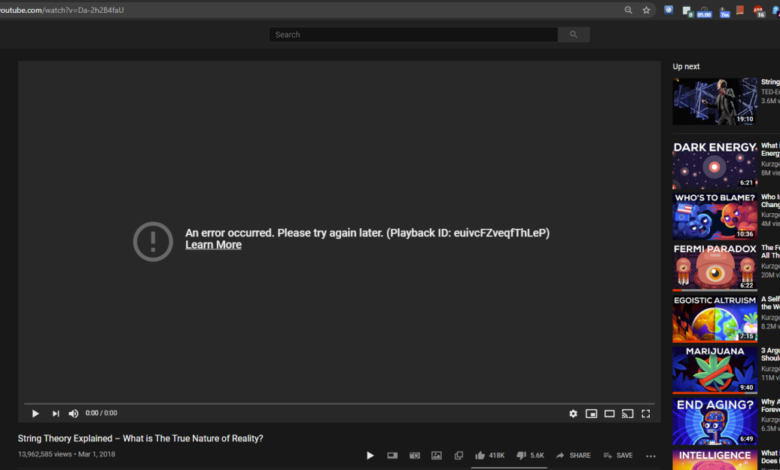
Frank Auerbach One Memorable Image
Frank auerbach aimed only at one memorable image – Frank Auerbach: One Memorable Image – that’s the core of his artistic philosophy. Forget sprawling narratives; Auerbach’s power lies in the single, arresting image, a moment captured with breathtaking intensity. He wasn’t interested in telling a story; he was obsessed with conveying the raw, visceral feeling of a place, a person, a fleeting emotion. This focus on the singular, unforgettable image shaped his entire career, demanding a unique approach to painting and a profound understanding of his chosen medium.
His technique, characterized by thick impasto and repeated layering of paint, reflects this pursuit. Each brushstroke is deliberate, building up a surface that pulsates with energy and texture. It’s a physical manifestation of the artist’s struggle to capture the essence of his subject, a battle between the fleeting moment and the enduring power of paint. The result is art that demands attention, that lingers in the mind long after you’ve looked away.
Auerbach’s Artistic Philosophy: Frank Auerbach Aimed Only At One Memorable Image
Frank Auerbach’s artistic philosophy centers on the immediate, visceral experience of painting. He eschews narrative or symbolic elements, instead focusing on the creation of a single, powerful image that encapsulates the essence of his subject. This commitment to the “memorable image” isn’t about capturing a fleeting moment, but rather about distilling the essence of form and presence through intense, repeated engagement with the model or landscape.
The resulting works are intensely physical, embodying the artist’s struggle and the very act of creation.Auerbach’s preference for single, powerful images contrasts sharply with more narrative-driven approaches. He’s not interested in telling a story; his paintings are not windows into a scene but rather intense explorations of form, texture, and light. The viewer’s experience is immediate and direct, focusing on the raw energy and physicality of the paint itself, rather than on deciphering a complex narrative.
This directness is what makes his images so memorable—they bypass intellectual interpretation and engage the viewer on a purely sensory level.
Technical Aspects Contributing to Impact, Frank auerbach aimed only at one memorable image
Auerbach’s distinctive impasto technique is fundamental to the impact of his memorable images. He applies paint thickly, building up layers upon layers in a process of constant reworking and revision. This layering creates a remarkable textural richness, with the surface of the painting becoming almost sculptural. The viewer can almost feel the physicality of the paint, its weight and density.
The visible brushstrokes, often heavily impastoed and seemingly uncontrolled, further emphasize the artist’s physical engagement with the canvas. His palette, often muted and earth-toned, contributes to the raw, almost primal feeling of his works. He uses colors not for their decorative effect, but to define form and volume, enhancing the three-dimensionality of his subjects. The resulting image is not a polished representation of reality, but a tangible record of the artist’s intense engagement with his subject and the physical act of painting.
Auerbach’s dedication to the single, memorable image isn’t just a stylistic choice; it’s a testament to the enduring power of focused observation and relentless artistic pursuit. He challenges us to look beyond the surface, to see the depth and complexity within the seemingly simple. His paintings are not just representations of reality; they are visceral experiences, emotional echoes that resonate long after the initial viewing.
The legacy of Frank Auerbach isn’t just a body of work, but a powerful reminder of the transformative potential of a single, perfectly realized image.
Frank Auerbach’s singular focus on capturing a single, powerful image reminds me of how focused certain political narratives can be. It’s like reading about how James Breslo argues that California, in an article james breslo california sides with criminals over law order and police again , consistently prioritizes a specific viewpoint, much like Auerbach’s unwavering commitment to his chosen subject.
This unwavering focus, whether artistic or political, can create a lasting impression, for better or worse.
Frank Auerbach’s singular focus on capturing a single, potent image reminds me of the incredible rarity of things. It makes me think about the recent news where miners found a new extraterrestrial mineral in Israel, miners discover new extraterrestrial mineral in israel worth more than diamonds , a discovery as unique and striking as one of Auerbach’s powerful portraits.
That kind of singular, breathtaking event echoes the deliberate intentionality in Auerbach’s art.
Frank Auerbach’s singular focus on capturing a single, powerful image reminds me of the laser-like intensity of investigations. The recent revelation that the US government’s filter team disclosed potentially privileged Trump records to case agents, as reported in this article , highlights a similar concentration of effort, albeit with far-reaching legal consequences. Just like Auerbach’s brushstrokes, these actions aim for a decisive, if controversial, outcome.