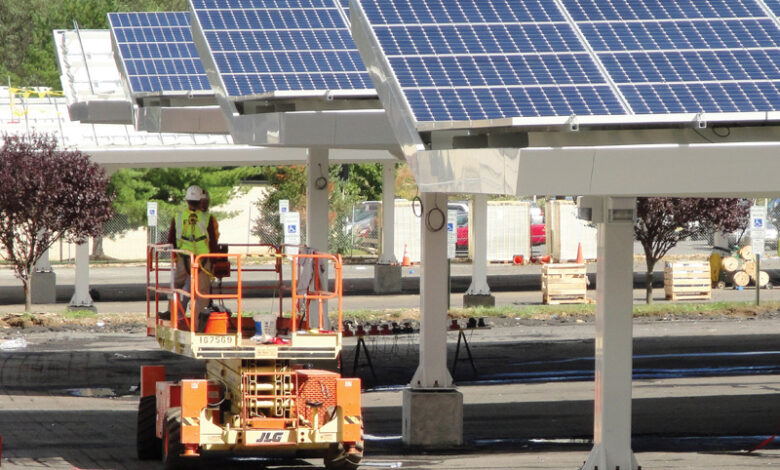
Node Names Dont Reflect Actual Transistor Sizes
Node names do not reflect actual transistor sizes – a seemingly simple statement, yet it unlocks a fascinating world of semiconductor manufacturing complexities. We’re used to hearing about 5nm, 3nm, and even 2nm processes, conjuring images of ever-shrinking transistors. But the reality is far more nuanced. This post dives into the discrepancies between these marketing-friendly node names and the actual physical dimensions of the transistors they represent, exploring the historical context, the implications for chip performance and power consumption, and the innovative solutions being developed to bridge this gap.
The seemingly straightforward naming convention hides a complex interplay of factors. Manufacturing processes aren’t perfect; variations in transistor size occur, and manufacturers employ various techniques to optimize performance and yield. This leads to a situation where a “5nm” process might actually involve transistors with significantly varying dimensions, impacting everything from clock speeds and power efficiency to overall chip design strategies.
Understanding this discrepancy is key to grasping the true advancements in semiconductor technology.
The Discrepancy Between Node Names and Transistor Sizes
The semiconductor industry’s node naming convention, while seemingly straightforward, masks a complex reality. The names, like 7nm, 5nm, and 3nm, initially suggested a direct correlation with the physical dimensions of the transistors. However, this simple interpretation quickly breaks down as advancements in manufacturing push the boundaries of miniaturization. This discrepancy between node names and actual transistor sizes is a significant aspect of understanding modern chip manufacturing.
Historical Context of Node Naming Conventions
Historically, node names directly reflected the minimum feature size, often the gate length of the transistors. Early processes, like the 1 µm node, accurately represented the physical dimensions. As technology progressed and manufacturing techniques became more sophisticated, this direct correlation began to erode. The industry clung to the node naming scheme for marketing and communication simplicity, even as the actual transistor dimensions diverged from the node number.
This created a disconnect between the marketing language and the underlying technological realities.
Factors Influencing Actual Transistor Size
Several factors contribute to the disparity between the node name and the actual transistor size. These include advancements in photolithography, the introduction of extreme ultraviolet (EUV) lithography, multiple patterning techniques (using different layers to create smaller features), and the use of finFETs (fin field-effect transistors) and GAAFETs (gate-all-around field-effect transistors). These techniques allow for the creation of smaller and more efficient transistors without necessarily reducing the minimum feature size to the number reflected in the node name.
For example, a 5nm node might employ multiple patterning to create transistors with gate lengths significantly smaller than 5nm, but the overall node name remains “5nm” for marketing purposes. Furthermore, the definition of “transistor size” itself is ambiguous; it could refer to the gate length, the overall transistor area, or other relevant dimensions.
Comparison of Node Naming Schemes
Different semiconductor manufacturers employ slightly varying approaches to node naming. While the general trend is towards smaller numbers representing more advanced nodes, there’s no universal standardization. For example, a 5nm node from one manufacturer might not be directly comparable to a 5nm node from another. This lack of uniformity adds to the confusion surrounding the relationship between node names and actual transistor dimensions.
The marketing strategy of each manufacturer also plays a role, with companies sometimes using different naming conventions to highlight their technological advantages.
It’s easy to get caught up in the hype around 3nm or 5nm nodes, but remember those names are marketing, not a precise measure of transistor size. The real implications are far more complex, as highlighted by the recent news that China is attempting to acquire a German semiconductor factory after the latest US chip ban – china moves to buy german semiconductor factory after new us chip ban – a move that underscores the intense global competition for advanced chip manufacturing capabilities, regardless of the somewhat misleading node naming conventions.
Ultimately, understanding the actual transistor performance, not just the marketing node name, is key to navigating this complex landscape.
Discrepancy Between Node Names and Transistor Sizes Across Manufacturers
The following table illustrates the discrepancy between node names and actual transistor sizes for three different manufacturers and three different nodes. Note that the data presented here is a simplified representation and precise figures are often proprietary and not publicly released. The values are estimations based on publicly available information and industry analysis.
It’s a common misconception that smaller node names in chip manufacturing always mean smaller transistors. The reality is much more nuanced. Thinking about this reminds me of a completely different logistical challenge: figuring out how to ship something delicate, like if you needed to know how to send a cake from New Jersey to Accra.
It’s all about careful planning and understanding the complexities involved, just like with those seemingly tiny transistors! Ultimately, node names are a simplification, not a precise measure of transistor size.
Node Name | Manufacturer | Transistor Gate Length (nm) | Transistor Area (nm²) |
---|---|---|---|
5nm | TSMC | ~3.5 | ~40 |
5nm | Samsung | ~4 | ~50 |
5nm | Intel | ~4.5 | ~60 |
7nm | TSMC | ~5 | ~70 |
7nm | Samsung | ~6 | ~80 |
7nm | Intel | ~6.5 | ~90 |
10nm | TSMC | ~7 | ~100 |
10nm | Samsung | ~8 | ~120 |
10nm | Intel | ~9 | ~150 |
Impact of the Discrepancy on Performance and Power Consumption
The mismatch between advertised node names (like 7nm, 5nm, 3nm) and the actual transistor sizes significantly impacts chip performance and power consumption. While node names provide a convenient shorthand, they don’t fully capture the complex realities of modern chip manufacturing. This discrepancy stems from various factors, including the evolving definitions of “node” itself and the continuous miniaturization challenges faced by chip manufacturers.
Understanding this impact is crucial for evaluating the true capabilities of modern processors and other integrated circuits.The difference between the named node and the actual transistor size directly influences chip performance. Smaller transistors generally allow for higher transistor density, leading to more transistors packed onto a chip. This increased density translates to greater processing power, enabling faster clock speeds and improved instruction-per-clock (IPC) performance.
It’s funny how those tiny node names in chip specs don’t really tell the whole story about transistor size; it’s all about marketing, really. Think about it – the sheer energy involved in manufacturing those things, enough to power a small city, which makes the news about britains last coal fired power station closes seem even more significant in the context of sustainable tech.
Ultimately, understanding the actual physical dimensions is key to grasping the true power efficiency, and that’s something those simplified node names just don’t convey.
However, the relationship isn’t strictly linear. As transistors shrink, various parasitic effects become more pronounced, limiting the speed gains. For example, leakage current increases significantly with smaller transistors, leading to higher power consumption and potentially reducing performance if not properly managed. This is why advanced process nodes often require sophisticated power management techniques.
Transistor Size and Power Consumption, Node names do not reflect actual transistor sizes
The relationship between transistor size and power consumption is complex and non-linear. Smaller transistors, while offering higher density, tend to consume more power per transistor due to increased leakage current. This is because the thinner gate oxide in smaller transistors allows more electrons to tunnel through, leading to higher standby power. Moreover, the increased density means more transistors are switching simultaneously, further increasing dynamic power consumption.
Consequently, while a smaller node might offer a theoretical performance boost, the overall power efficiency may not improve proportionally. Efficient power management techniques like advanced sleep states, voltage scaling, and specialized circuit designs are crucial to mitigate this increased power consumption. A higher power consumption can lead to increased heat generation, requiring larger and more sophisticated cooling solutions.
Impact on Specific Applications
This discrepancy between node names and actual transistor sizes significantly impacts various applications. In high-performance computing (HPC), where every bit of performance matters, the discrepancy can translate to noticeable differences in computational speed and energy efficiency. For instance, a supercomputer utilizing chips built on a “5nm” node might not achieve the performance gains expected based solely on the node name, due to the actual transistor dimensions being larger than advertised.
Similarly, in mobile devices, the power consumption implications are critical. A smartphone processor based on a “3nm” node might still suffer from significant battery drain if the actual transistor size is larger than expected, leading to shorter battery life despite the advertised performance improvements. In energy-constrained applications like IoT devices, even small discrepancies in power consumption can significantly affect battery life and operational lifespan.
Advantages and Disadvantages of Smaller-than-Advertised Transistors
The following points highlight the potential advantages and disadvantages of employing transistors that are smaller than the node name suggests:
The impact of this discrepancy is a complex trade-off between performance and power efficiency. Manufacturers strive to optimize both, but the realities of manufacturing limitations and physical effects often mean that the advertised node name is a simplification of the actual technological achievements.
- Advantages: Increased transistor density, potentially leading to higher performance and more features on a chip. Improved power efficiency (if power management techniques are effectively implemented).
- Disadvantages: Increased leakage current and power consumption per transistor. Manufacturing challenges and higher costs associated with smaller transistors. Increased susceptibility to process variations and defects.
Implications for Chip Design and Manufacturing
The disconnect between the marketing names of process nodes and their actual transistor dimensions presents significant challenges for chip designers and manufacturers. This discrepancy forces them to grapple with unexpected variations in transistor performance and power consumption, demanding innovative design strategies and advanced manufacturing techniques to ensure the success of their chips. The consequences ripple through the entire design and manufacturing process, impacting everything from initial design choices to final yield.The mismatch between node names and physical dimensions leads to several key challenges.
Designers must account for the larger-than-expected variations in transistor characteristics, which can affect circuit performance and reliability. This uncertainty necessitates more rigorous verification and validation processes, increasing design complexity and time-to-market. Furthermore, power consumption can be harder to predict accurately, leading to potential overheating and reduced battery life in mobile devices. The unpredictable behavior of transistors at smaller nodes also necessitates more complex power management strategies.
Finally, increased process variations necessitate more sophisticated manufacturing techniques to maintain acceptable yield levels.
Challenges Faced by Chip Designers
The primary challenge is accurately predicting the performance and power consumption of a design when the actual transistor dimensions deviate from the nominal values implied by the node name. This requires more extensive simulations and testing throughout the design process. Moreover, designers must develop robust designs that can tolerate larger variations in transistor parameters than previously assumed. This necessitates the use of design techniques that are less sensitive to process variations, such as robust design methodologies and advanced circuit topologies.
For example, designers might employ techniques like statistical static timing analysis (SSTA) to account for process variations and ensure timing closure. They also might incorporate design-for-manufacturability (DFM) techniques to minimize the impact of process variations on yield. The increased complexity also necessitates more sophisticated design tools and flows, increasing the overall cost and complexity of chip development.
Strategies for Optimizing Chip Design
Manufacturers employ various strategies to mitigate the effects of the node name discrepancy. One common approach is to use more conservative design margins, which increases the chip area and potentially the cost. However, this approach ensures reliable operation despite variations in transistor performance. Another approach is to use advanced process control (APC) techniques to reduce the variations in transistor parameters during manufacturing.
This involves using real-time feedback from the manufacturing process to adjust process parameters and minimize variations. Furthermore, manufacturers utilize advanced design methodologies such as FinFET transistors, which offer improved control over transistor characteristics compared to older planar transistors. These advanced transistors can help to mitigate some of the challenges associated with the variations in transistor dimensions. Finally, techniques like multiple-VT (threshold voltage) designs, where transistors with different threshold voltages are used in the same design, are employed to optimize power and performance.
Comparison of Design Methodologies
Several design methodologies are employed to address the mismatch between node names and transistor dimensions. Traditional design methodologies rely heavily on nominal parameters and may not adequately account for process variations. More advanced methodologies, such as statistical static timing analysis (SSTA) and robust design techniques, explicitly consider process variations and aim to design circuits that are less sensitive to these variations.
SSTA incorporates statistical information about process variations into the timing analysis, allowing designers to assess the timing closure probability under various process conditions. Robust design methodologies employ techniques such as design centering and tolerance analysis to optimize the design for robustness against process variations. A comparison of these methodologies is shown below.
Methodology | Description | Advantages | Disadvantages |
---|---|---|---|
Traditional Design | Relies on nominal parameters. | Simpler, faster. | Vulnerable to process variations. |
SSTA | Incorporates statistical information about process variations. | More accurate timing analysis. | More complex, computationally expensive. |
Robust Design | Optimizes the design for robustness against process variations. | Improved yield and reliability. | May require larger chip area. |
Advanced Process Control Techniques
Advanced process control (APC) techniques play a crucial role in mitigating the effects of variations in transistor size. APC uses real-time feedback from the manufacturing process to adjust process parameters and minimize variations. For example, in-situ monitoring of critical process parameters during fabrication allows for immediate adjustments, minimizing deviations from the target values. This closed-loop control system helps to maintain consistent transistor characteristics across the wafer, improving yield and reducing the impact of process variations on chip performance.
Techniques such as metrology and advanced modeling are integral parts of APC, providing the necessary data for feedback and control. The implementation of APC requires significant investment in advanced manufacturing equipment and expertise, but the benefits in terms of improved yield and product quality often outweigh the costs.
Future Trends and Potential Solutions
The disconnect between semiconductor node names and actual transistor dimensions is a significant challenge for the industry. While the current naming scheme has historical context, its increasing inaccuracy hinders clear communication and complicates design and manufacturing processes. Fortunately, several potential solutions and future trends are emerging to address this issue. These range from revised naming conventions to innovative manufacturing techniques.The continued miniaturization of transistors, coupled with the complexity of modern chip architectures, makes it increasingly difficult to maintain a direct correlation between node names and physical dimensions.
Simply put, the traditional 7nm, 5nm, 3nm naming system is becoming less representative of the actual physical characteristics of the transistors. This necessitates a re-evaluation of how we communicate the advancements in chip technology.
Revised Node Naming Conventions
One promising avenue is the adoption of a more descriptive and transparent node naming convention. Instead of relying solely on a single number representing a nominal feature size, a multi-parameter system could be implemented. This might include parameters like gate length, fin height, and metal pitch, providing a more complete picture of the transistor’s physical characteristics. For example, a node could be designated as “12nm-Gate/5nm-Fin/20nm-Metal,” offering a far more nuanced understanding of its capabilities compared to a simple “12nm” label.
This increased transparency would aid in accurate comparisons between different technologies and manufacturers. Such a system would need industry-wide consensus to be truly effective, but the benefits in terms of clear communication are undeniable.
Innovative Approaches to Improve Correlation
Beyond revised naming, innovative manufacturing techniques can improve the correlation between node names and transistor sizes. Techniques like EUV lithography, which allows for finer feature sizes, are crucial. However, even with EUV, the inherent complexities of 3D transistor architectures (FinFETs, GAAFETs) make direct size correlation challenging. Further advancements in lithography techniques, coupled with innovative process control methods, will be vital in ensuring a closer relationship between the stated node and the actual transistor dimensions.
Improved process control could involve the use of advanced metrology techniques to provide more accurate measurements of transistor features, leading to better prediction and control during manufacturing.
The Role of Advanced Materials and Manufacturing Processes
The adoption of advanced materials plays a crucial role in resolving the discrepancy. New materials with superior electrical and mechanical properties can lead to smaller, more efficient transistors. For example, the exploration of new gate dielectrics and channel materials can significantly impact transistor performance and scaling. Furthermore, innovative manufacturing processes, such as self-aligned patterning and directed self-assembly, offer the potential for creating more precise and smaller transistor features.
These techniques reduce reliance on purely optical lithography, mitigating some of the limitations currently affecting size correlation.
Potential Research Areas
The discrepancy between node names and transistor sizes necessitates focused research efforts. The following areas warrant significant attention:
- Development of more accurate and reliable metrology techniques for characterizing transistor dimensions and performance.
- Exploration of novel materials and fabrication processes for creating smaller, more efficient transistors.
- Investigation of advanced lithography techniques beyond EUV, such as directed self-assembly and nanoimprint lithography.
- Development of new simulation and modeling tools to accurately predict transistor behavior at advanced nodes.
- Creation of standardized metrics and benchmarks for evaluating and comparing different semiconductor technologies.
Illustrative Examples: Node Names Do Not Reflect Actual Transistor Sizes
The discrepancy between node names and actual transistor sizes, while seemingly a technical detail, has significant real-world consequences. Ignoring this discrepancy can lead to unexpected performance bottlenecks, increased power consumption, and ultimately, failed product launches. Let’s explore some hypothetical scenarios to illustrate these points.Let’s imagine a hypothetical scenario involving the development of a high-performance computing (HPC) cluster for scientific simulations.
The design team, relying solely on the marketing-driven node name (e.g., “5nm”), might underestimate the actual transistor size and resulting power density. This could lead to an overly dense chip design, resulting in excessive heat generation. The cooling infrastructure designed around the projected power consumption might prove inadequate, causing system instability and reduced performance. The resulting simulations would take significantly longer than expected, delaying crucial scientific breakthroughs.
This is a costly failure, not only financially but also in terms of lost research time.
High-Performance Computing Cluster Design
In our HPC cluster scenario, the design team initially projected a power consumption of 100W per chip based on the advertised “5nm” node. However, due to the discrepancy between the advertised node and the actual transistor size (let’s say the effective size is closer to 6nm), the actual power consumption per chip ends up being 120W. This 20% increase in power consumption significantly impacts the overall system design.
The cooling system, originally designed for 100W per chip, now needs to handle 120W, requiring more powerful fans, potentially larger heat sinks, and a more sophisticated cooling solution. This adds considerable cost and complexity to the final product. Furthermore, the increased power consumption might also lead to reduced battery life in portable applications or increased operational costs in data centers.
The additional heat generation could also lead to accelerated degradation of the chips themselves, reducing their lifespan.
High-Volume Manufacturing Trade-offs
Managing the impact of this discrepancy in high-volume manufacturing necessitates careful consideration of various design trade-offs. For instance, a conservative design approach might involve using larger transistors than strictly necessary to reduce power density and heat generation. However, this approach compromises the potential performance gains associated with smaller transistors and can increase the overall chip area, leading to higher manufacturing costs.
Alternatively, a more aggressive design approach might utilize smaller transistors but necessitate a more sophisticated cooling solution and more stringent testing procedures to ensure reliability. This, in turn, could also impact manufacturing yield and increase the overall cost per unit. The optimal strategy involves a complex balancing act between performance, power consumption, manufacturing cost, and yield. The choice depends on various factors including the target market, the application’s requirements, and the overall manufacturing capabilities.
For example, a high-end server chip might justify a more aggressive approach with enhanced cooling, while a low-power mobile device might prioritize reduced power consumption over maximum performance.
So, the next time you hear about a new “X nm” process, remember that it’s not just about the number. The reality is far more intricate, involving compromises between transistor size, performance, power consumption, and manufacturing yield. The discrepancy between node names and actual transistor sizes highlights the incredible ingenuity and complexity behind modern chip manufacturing. While the marketing may simplify things, the underlying engineering challenges are constantly pushing the boundaries of what’s possible, driving innovation in materials science, manufacturing processes, and chip design methodologies.
The future of semiconductor technology hinges on overcoming these challenges and achieving even tighter control over transistor dimensions.