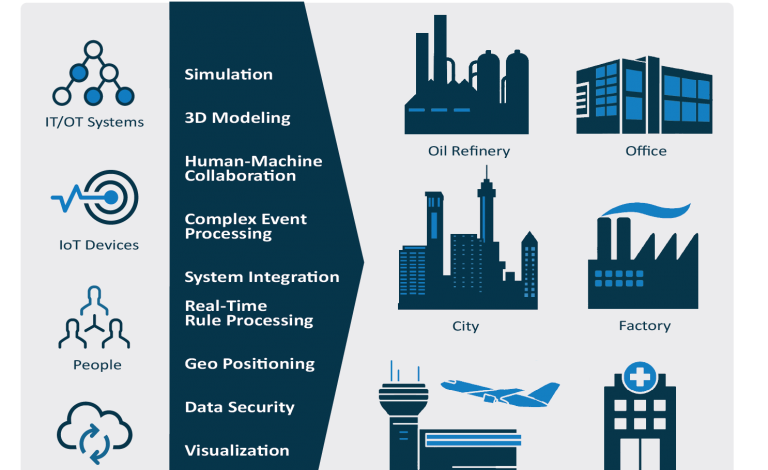
Digital Twins Are Making Companies More Efficient
Digital twins are making companies more efficient – it’s a statement that’s quickly moving from futuristic concept to everyday reality. These virtual representations of physical assets and processes are revolutionizing how businesses operate, offering unprecedented insights and opportunities for optimization. Imagine having a perfect digital mirror of your factory floor, predicting potential equipment failures before they happen, or simulating different supply chain scenarios to identify bottlenecks and optimize logistics.
That’s the power of digital twins, and it’s transforming industries at an incredible pace.
From streamlining manufacturing processes to enhancing predictive maintenance and improving supply chain resilience, digital twins offer a wealth of benefits. By analyzing vast amounts of real-time data, these virtual models provide actionable insights that lead to tangible efficiency gains, reduced costs, and improved decision-making. We’ll explore real-world examples, delve into the underlying technologies, and examine the challenges and future potential of this transformative technology.
Defining Digital Twins and Efficiency Gains
Digital twins are virtual representations of physical objects, processes, or systems. They leverage data from various sources to create a dynamic, constantly updating model that mirrors its real-world counterpart. This allows businesses to simulate scenarios, predict potential problems, and optimize performance in a risk-free environment, ultimately leading to significant efficiency gains.Digital twins function by integrating data from multiple sources, including sensors embedded in physical assets, operational data from manufacturing processes, and external data like weather patterns or market trends.
Core components typically include a data acquisition layer, a modeling engine that simulates the behavior of the twin, and a user interface that allows for visualization and interaction. The accuracy and effectiveness of a digital twin are directly related to the quality and quantity of data it incorporates.
Operational Efficiency Improvements Through Digital Twins
Digital twins contribute to increased operational efficiency in several key ways. They enable predictive maintenance by analyzing sensor data to identify potential equipment failures before they occur, minimizing downtime and reducing maintenance costs. They facilitate process optimization by simulating different scenarios and identifying bottlenecks or inefficiencies in workflows. Real-time monitoring capabilities allow for immediate responses to unexpected events, improving overall system resilience.
Furthermore, digital twins can be used for training and simulation, allowing operators to practice complex procedures in a safe and controlled environment.
Examples of Digital Twin Applications Across Industries
The application of digital twins is rapidly expanding across various industries, driving significant improvements in efficiency. Below is a table illustrating some key examples:
Industry | Specific Application of Digital Twin | Efficiency Improvement | Quantifiable Results |
---|---|---|---|
Manufacturing | Predictive maintenance of assembly lines, optimizing production schedules | Reduced downtime, improved resource allocation | 15% reduction in unplanned downtime, 10% increase in production output (example based on a case study of a large automotive manufacturer) |
Energy | Monitoring and optimizing performance of wind turbines, predicting energy output | Increased energy production, reduced maintenance costs | 5% increase in energy yield, 20% reduction in maintenance costs (example based on a study of a wind farm operator) |
Healthcare | Simulating surgical procedures, personalized drug development | Improved surgical outcomes, faster drug development | 10% reduction in surgical complications, 25% reduction in drug development time (example based on research into digital twin applications in surgery and drug development) |
Aerospace | Simulating aircraft performance, predicting maintenance needs | Improved flight safety, reduced maintenance costs | 5% reduction in fuel consumption, 10% reduction in maintenance costs (example based on a case study of an airline using digital twins for aircraft maintenance) |
Real-World Applications of Digital Twins for Efficiency
Digital twins are no longer a futuristic concept; they’re actively transforming industries, driving significant efficiency gains for businesses of all sizes. By creating virtual representations of physical assets or processes, companies can simulate, analyze, and optimize their operations in ways previously unimaginable, leading to cost savings, reduced downtime, and improved product quality. This section will explore real-world examples showcasing the transformative power of digital twins in enhancing operational efficiency.Companies are leveraging digital twins to solve complex challenges and unlock new levels of performance.
The benefits extend across various sectors, from manufacturing and supply chain management to healthcare and urban planning. The common thread is the ability to gain unprecedented insight into system behavior, allowing for proactive interventions and data-driven decision-making.
Digital Twin Implementation in Manufacturing: GE’s Gas Turbine Optimization
GE has successfully utilized digital twins to optimize its gas turbine engines. By creating a virtual representation of the engine, GE engineers can simulate various operating conditions, predict potential failures, and optimize maintenance schedules. This has led to significant reductions in downtime and maintenance costs. For instance, they can identify potential issues before they manifest physically, allowing for proactive repairs and preventing costly unplanned outages.
The digital twin also enables testing of new designs and operational strategies in a virtual environment, minimizing risks and accelerating innovation. This approach allows for more efficient use of resources and reduces the reliance on costly physical testing.
Digital Twins in Supply Chain Management: Optimizing Logistics at Maersk
Maersk, a global shipping giant, employs digital twins to enhance its supply chain efficiency. Their digital twin models simulate various scenarios, including port congestion, weather patterns, and demand fluctuations. This allows them to optimize shipping routes, predict potential delays, and proactively adjust their logistics operations to minimize disruptions. By analyzing data from various sources, including vessel sensors, weather forecasts, and port information, Maersk can improve its decision-making, reduce fuel consumption, and enhance overall delivery times.
The ability to anticipate and mitigate potential issues leads to significant cost savings and improved customer satisfaction.
Hypothetical Scenario: Optimizing Warehouse Operations with a Digital Twin
Imagine a large e-commerce warehouse struggling with inefficient order fulfillment. A digital twin of the warehouse could be created, incorporating data on product locations, worker movements, order volume, and equipment performance. This virtual model would allow for simulations of various scenarios, such as optimizing the layout of the warehouse, improving the routing of picking carts, and predicting peak demand periods.
By analyzing the data generated by the digital twin, managers could identify bottlenecks, optimize resource allocation, and implement changes to improve order fulfillment speed and accuracy. For example, the simulation might reveal that relocating a high-demand product closer to the shipping area would significantly reduce picking times, leading to faster order fulfillment and increased customer satisfaction. The digital twin allows for testing these changes virtually before implementing them physically, minimizing disruption and maximizing the impact of improvements.
Data Analysis and Predictive Capabilities of Digital Twins: Digital Twins Are Making Companies More Efficient
Digital twins aren’t just virtual replicas; they’re powerful analytical tools capable of transforming how businesses operate. By leveraging the vast amounts of data generated by their physical counterparts, digital twins unlock predictive capabilities that drive efficiency and prevent costly downtime. This data-driven approach allows for proactive problem-solving, optimizing processes, and ultimately, maximizing profitability.The effectiveness of a digital twin hinges heavily on the quality and analysis of the data it receives.
Sophisticated data analytics techniques are employed to extract meaningful insights from sensor data, operational logs, and other relevant sources. This processed information forms the basis for monitoring key performance indicators (KPIs), identifying potential issues, and predicting future performance. Without robust data analytics, the digital twin remains a static model, failing to realize its full potential.
Digital twins are revolutionizing efficiency across industries, optimizing processes from manufacturing to logistics. It’s fascinating to see how precise modeling can improve outcomes, much like understanding the nuances of vaccine reactions, as highlighted in a recent study: new study finds heart inflammation after covid 19 vaccination higher with moderna than pfizer. This level of data-driven precision mirrors the benefits companies see when implementing digital twin technology; both require careful analysis to achieve optimal results.
Key Performance Indicators (KPIs) Monitored and Improved Using Digital Twins
The selection of KPIs depends on the specific application of the digital twin. However, some common examples applicable across various industries illustrate the power of this technology. Careful monitoring of these metrics enables proactive interventions, preventing minor issues from escalating into major problems.
Digital twins are revolutionizing industries, offering unprecedented efficiency gains through predictive modeling and optimization. It’s fascinating to consider how this technological leap contrasts with the political landscape; while companies streamline operations, the article, europeans are facing the prospect of trump like a deer caught in headlights , highlights a very different kind of uncertainty. Ultimately, though, both scenarios underscore the importance of adapting to change and leveraging available tools – whether that’s digital twins or strategic political maneuvering – for better outcomes.
- Overall Equipment Effectiveness (OEE): This measures the percentage of time a machine is producing good parts. A digital twin can identify factors affecting OEE, such as downtime, speed reduction, and quality defects, allowing for timely maintenance and process optimization.
- Mean Time Between Failures (MTBF): This KPI indicates the average time between equipment failures. By analyzing historical data and simulating different scenarios within the digital twin, companies can predict potential failures and schedule preventative maintenance, minimizing disruptions.
- Energy Consumption: Digital twins can track energy usage in real-time, identifying areas of inefficiency. This allows for optimization strategies, leading to cost savings and reduced environmental impact. For example, a digital twin of a manufacturing plant might reveal that specific machinery consumes significantly more energy than expected, prompting an investigation into potential mechanical issues or process improvements.
- Production Yield: This KPI measures the output compared to the planned production. A digital twin can analyze various factors influencing yield, such as material quality, process parameters, and equipment performance, and suggest adjustments to improve overall efficiency. For instance, a slight adjustment in temperature or pressure predicted by the digital twin might significantly increase yield without compromising quality.
- Inventory Levels: Digital twins can optimize inventory management by accurately predicting demand based on historical data and real-time sales figures. This minimizes storage costs and prevents stockouts or overstocking.
Predictive Modeling and Issue Prevention
Predictive modeling, a core capability of digital twins, allows for proactive problem-solving. By analyzing historical data and simulating various scenarios, the digital twin can predict potential issues before they occur. This allows for timely interventions, preventing costly downtime and improving overall efficiency. For example, a digital twin of a wind turbine might predict a potential gear failure based on vibration patterns and operational data, allowing for preventative maintenance to be scheduled before the failure occurs, avoiding costly repairs and potential energy loss.
Digital twins are revolutionizing efficiency across industries, allowing for predictive maintenance and optimized resource allocation. This is especially crucial in sectors like renewable energy, which is poised to become, as this article explains, clean energy’s next trillion dollar business. The ability to model and simulate complex systems with digital twins will be key to unlocking the full potential of clean energy and, in turn, further boosting the efficiency gains companies are already experiencing.
This predictive capability is far superior to reactive maintenance, which only addresses issues after they have occurred.
“The ability to predict potential failures before they happen is a game-changer. It allows for proactive maintenance, reducing downtime and maximizing operational efficiency.”
Cost and Implementation Challenges of Digital Twins
The allure of increased efficiency and predictive capabilities through digital twins is undeniable. However, the journey to realizing these benefits isn’t without its hurdles. The cost of development and maintenance, coupled with various implementation challenges, can significantly impact a company’s decision to adopt this technology. Understanding these factors is crucial for successful deployment.The costs associated with creating and maintaining a digital twin vary dramatically depending on the complexity and scale of the project.
A simple digital twin for a small-scale manufacturing process might involve relatively modest investment in software and personnel, whereas a complex, enterprise-wide digital twin encompassing numerous interconnected systems could require substantial capital expenditure and ongoing operational costs. These costs encompass software licenses, hardware requirements (including powerful computing resources for data processing and simulation), data acquisition and integration, skilled personnel for development and maintenance, and ongoing data management.
Furthermore, the cost is not just financial; it includes the time commitment required for project planning, implementation, and ongoing monitoring and refinement.
Cost Comparison Across Different Scales of Implementation, Digital twins are making companies more efficient
Small businesses might leverage readily available software and internal expertise, resulting in lower initial investment. However, scalability and integration with existing systems can present challenges. Medium-sized businesses may require more sophisticated software and specialized consultants, leading to higher upfront costs but also enabling more advanced functionalities. Large enterprises often invest in custom-built digital twins, integrating data from numerous sources across their operations.
This leads to significantly higher costs but potentially unlocks substantial efficiency gains across their entire value chain. For example, a small bakery might create a digital twin of its oven using readily available sensor data and simple software, while a large automotive manufacturer might develop a comprehensive digital twin of its entire production line, requiring specialized software, high-performance computing, and a large team of engineers and data scientists.
The cost difference can be orders of magnitude.
Potential Obstacles and Challenges in Digital Twin Implementation
Implementing digital twins successfully requires careful planning and execution. Several obstacles can hinder the process. Data integration from disparate systems can be a significant challenge, requiring careful data cleansing, transformation, and harmonization. The lack of skilled personnel with expertise in data science, software development, and domain-specific knowledge can also limit successful implementation. Ensuring data security and privacy is paramount, especially when dealing with sensitive operational data.
Furthermore, the need for robust and reliable infrastructure, including high-bandwidth networks and powerful computing resources, adds to the complexity. Finally, obtaining buy-in from stakeholders across different departments is crucial for successful adoption and ongoing maintenance. Resistance to change and a lack of understanding of the benefits of digital twins can hinder the process.
Step-by-Step Implementation of a Digital Twin for a Small Business
A small business, let’s say a local coffee shop, wanting to implement a digital twin of its espresso machine could follow these steps:
- Define Objectives: Clearly identify the specific goals of the digital twin. For example, improving maintenance scheduling or optimizing the brewing process.
- Data Acquisition: Identify relevant data points to collect, such as machine temperature, pressure, and energy consumption. This might involve installing simple sensors on the espresso machine.
- Data Integration and Processing: Choose appropriate software (potentially cloud-based) to collect, store, and process the data. This could be a simple spreadsheet initially.
- Model Development: Create a simplified digital twin model based on the collected data. This might be a simple simulation of the espresso machine’s operation.
- Validation and Refinement: Compare the model’s predictions with real-world observations to ensure accuracy and make necessary adjustments.
- Deployment and Monitoring: Integrate the digital twin into the coffee shop’s workflow and continuously monitor its performance.
This phased approach allows for iterative improvement and minimizes the risk of large-scale failures. The coffee shop can gradually expand the capabilities of its digital twin as needed and as its resources allow.
Future Trends and Developments in Digital Twin Technology
The world of digital twins is rapidly evolving, driven by advancements in interconnected technologies and the increasing demand for enhanced efficiency across various sectors. We’re moving beyond simple representations to incredibly sophisticated, dynamic models capable of predicting and optimizing complex systems with unprecedented accuracy. This evolution promises to reshape industries and redefine how we approach problem-solving and resource management.The convergence of artificial intelligence (AI), the Internet of Things (IoT), and robust cloud computing infrastructure is fueling this transformation.
These technologies are not merely supplementary; they are fundamental to the next generation of digital twins. AI empowers digital twins with advanced analytical capabilities, enabling them to learn from data, identify patterns, and make predictions with greater precision. IoT provides the continuous stream of real-time data that feeds these AI algorithms, creating a closed-loop system of observation, analysis, and action.
Cloud computing provides the scalable infrastructure needed to handle the massive datasets and complex computations involved.
Enhanced Capabilities Through AI, IoT, and Cloud Computing
AI algorithms are being integrated into digital twins to enhance their predictive capabilities. For example, machine learning models can analyze historical and real-time data from a manufacturing plant’s digital twin to predict potential equipment failures, allowing for proactive maintenance and minimizing downtime. This predictive maintenance is a significant step towards greater efficiency and cost savings. Furthermore, AI-powered optimization algorithms can analyze the digital twin’s data to identify inefficiencies in processes and suggest improvements, leading to streamlined operations and reduced waste.
The seamless integration of IoT sensors provides the necessary data influx for AI to function effectively. Cloud computing provides the necessary scalable infrastructure for storing and processing the vast amounts of data generated by these interconnected systems.
Impact on Various Industries
The impact of advanced digital twins will be felt across a broad spectrum of industries. In manufacturing, digital twins will optimize production lines, predict equipment failures, and improve product design. In healthcare, they will enable personalized medicine, improve surgical planning, and accelerate drug discovery. In the energy sector, they will optimize power grids, predict energy demand, and improve the efficiency of renewable energy sources.
The transportation industry will see improvements in logistics, autonomous vehicle development, and traffic management. Even in urban planning, digital twins of cities can help optimize traffic flow, manage resources, and improve the quality of life for citizens.
Futuristic Application: Smart City Management
Imagine a futuristic city where a comprehensive digital twin manages every aspect of urban life. This digital twin, powered by AI, IoT, and cloud computing, would integrate data from various sources, including traffic sensors, weather stations, energy grids, and public transportation systems. It would predict traffic congestion and dynamically adjust traffic signals to optimize flow, reducing commute times and emissions.
It would monitor energy consumption and adjust energy distribution to minimize waste and maximize the use of renewable energy sources. The digital twin would also manage waste disposal, predict public health risks, and optimize resource allocation. This sophisticated system would enhance the efficiency of city operations, improve the quality of life for citizens, and create a more sustainable urban environment.
Such a system could significantly reduce traffic congestion by up to 30% in peak hours, based on simulations using existing traffic management systems enhanced with AI and real-time data. Energy consumption could be optimized by 15-20%, leading to significant cost savings and reduced carbon footprint. This level of efficiency enhancement is projected based on current trends in smart city technology and the increasing capabilities of digital twins.
The journey into the world of digital twins reveals a compelling narrative of efficiency and innovation. We’ve seen how these virtual counterparts are not just mirroring reality, but actively shaping it, leading to significant improvements across various industries. While challenges remain in terms of implementation and cost, the potential benefits – from reduced downtime and optimized resource allocation to enhanced predictive capabilities and proactive problem-solving – are undeniable.
As technology continues to evolve, digital twins will undoubtedly play an even more crucial role in driving operational excellence and shaping the future of business.