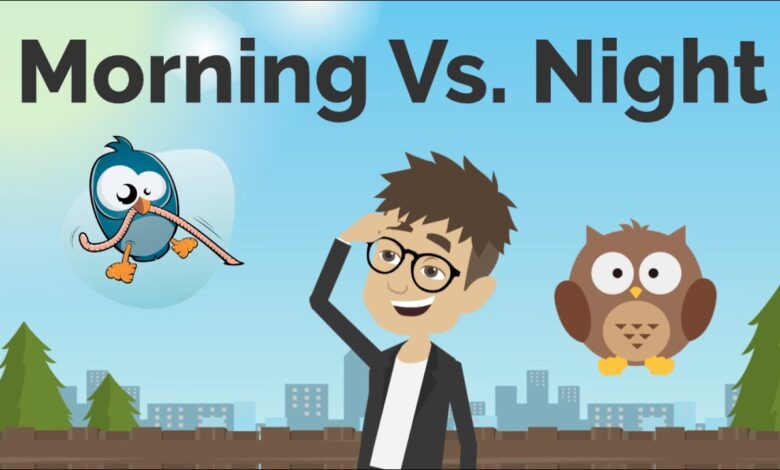
Digital Twins Are Speeding Up Manufacturing
Digital twins are speeding up manufacturing – it’s a bold statement, but increasingly true! Imagine a perfect digital replica of your entire factory, humming along in a virtual world, predicting problems before they even arise and optimizing every process for maximum efficiency. That’s the power of digital twins, and it’s revolutionizing how we build, produce, and deliver goods.
This technology allows manufacturers to simulate real-world scenarios, test new processes, and identify potential bottlenecks, all without disrupting actual production. From predictive maintenance that minimizes downtime to streamlined production planning that maximizes output, the benefits are substantial and far-reaching. We’ll delve into specific examples, explore the tech behind it all, and even look at the future of this exciting field.
Defining Digital Twins in Manufacturing: Digital Twins Are Speeding Up Manufacturing
Digital twins are revolutionizing manufacturing, offering unprecedented opportunities for optimization and efficiency. Essentially, a digital twin is a virtual representation of a physical object or process, mirroring its behavior and characteristics throughout its lifecycle. In manufacturing, this means creating a virtual replica of a product, a production line, or even the entire factory, allowing manufacturers to simulate, analyze, and optimize various aspects of their operations before implementing changes in the real world.
This proactive approach significantly reduces risks, minimizes downtime, and accelerates innovation.
Core Concept of Digital Twins in Manufacturing
At its heart, a manufacturing digital twin leverages data from various sources – sensors embedded in machinery, CAD models, production schedules, and even real-time operational data – to create a dynamic, up-to-the-minute virtual model. This model isn’t just a static 3D representation; it’s a living, breathing simulation that continuously updates based on real-world events. This allows manufacturers to predict potential problems, test different scenarios, and optimize processes for maximum efficiency and quality.
For example, a digital twin of a specific machine could predict maintenance needs based on its operating parameters, preventing unexpected breakdowns and costly downtime.
Key Components of a Digital Twin System
A comprehensive digital twin system in manufacturing typically consists of several interconnected components. These include: a data acquisition layer (collecting data from various sources), a data processing and analytics layer (cleaning, transforming, and analyzing the data), a simulation and modeling layer (creating and updating the virtual model), a visualization layer (presenting the data and simulations in an understandable format), and an integration layer (connecting the digital twin to other systems, such as ERP and MES).
Each layer plays a critical role in the overall effectiveness of the digital twin. The integration of these components is key to realizing the full potential of this technology.
Types of Digital Twins in Manufacturing
Different types of digital twins cater to specific needs within a manufacturing environment. A product digital twin simulates the performance and behavior of a specific product throughout its lifecycle, from design and manufacturing to operation and disposal. A process digital twin focuses on modeling and optimizing individual manufacturing processes, such as assembly or machining. Finally, a system digital twin represents the entire manufacturing system, encompassing all machines, processes, and resources.
Each type offers unique advantages depending on the specific application and objectives. For instance, a product digital twin could be used to simulate the effects of different materials on product durability, while a system digital twin might be used to optimize the flow of materials through the entire factory.
Advantages and Disadvantages of Implementing Digital Twins, Digital twins are speeding up manufacturing
Implementing digital twins offers significant benefits but also presents challenges.
Advantage | Disadvantage |
---|---|
Improved efficiency and productivity | High initial investment costs |
Reduced downtime and maintenance costs | Complexity of implementation and integration |
Enhanced product quality and reliability | Need for skilled personnel and expertise |
Faster time-to-market | Data security and privacy concerns |
Speed Improvements Enabled by Digital Twins
Digital twins are revolutionizing manufacturing by offering a virtual representation of physical assets and processes. This allows manufacturers to test, analyze, and optimize their operations in a simulated environment, leading to significant speed improvements across various stages of production. The ability to predict and prevent problems before they occur, coupled with the power of real-time data analysis, translates directly into faster production cycles and reduced lead times.Digital twins demonstrably accelerate processes by providing a platform for comprehensive analysis and optimization across several key areas.
This virtual mirroring allows for rapid experimentation and iterative improvements, ultimately streamlining production and boosting efficiency. The speed gains aren’t merely incremental; they represent a fundamental shift towards a more agile and responsive manufacturing paradigm.
Faster Troubleshooting and Reduced Downtime
Digital twins enable rapid identification and resolution of production line issues. By simulating various scenarios, engineers can pinpoint the root cause of malfunctions much faster than traditional methods. For instance, imagine a bottling plant experiencing inconsistent fill levels. A digital twin could simulate different factors – from the speed of the filling mechanism to variations in bottle weight – to isolate the problem, potentially revealing a faulty sensor or a need for minor adjustments to the filling line.
This rapid diagnosis translates directly into minimized downtime and faster restoration of optimal production levels. Instead of hours spent on physical inspection and trial-and-error, the issue can be resolved within minutes, significantly boosting overall productivity.
Predictive Maintenance and Its Impact on Speed
Predictive maintenance, powered by digital twin technology, is a game-changer for maintaining production speed. By analyzing sensor data from the physical asset and simulating its behavior under different conditions, the digital twin can predict potential equipment failures before they occur. This allows for proactive maintenance scheduling, preventing unexpected breakdowns that halt production lines. For example, a wind turbine manufacturer might use a digital twin to predict blade fatigue based on wind speed and operational data.
Digital twins are revolutionizing manufacturing, optimizing processes and reducing waste. It’s crazy to think about that level of efficiency alongside the frankly appalling news I just read – check out this article about senator sanders plan to fight climate change with third world population control is disgusting stuart varney – it makes you appreciate the focus on sustainable practices that digital twins can help facilitate.
Ultimately, efficient manufacturing, aided by digital twins, is crucial for a greener future.
This allows for timely maintenance, preventing costly and time-consuming repairs and ensuring uninterrupted power generation. The predictive capabilities offered by digital twins reduce downtime, resulting in significantly faster overall production cycles.
Optimized Production Planning and Scheduling Through Simulation
Digital twins provide a powerful environment for simulating different production scenarios, optimizing planning and scheduling. By inputting various parameters such as material availability, machine capacity, and order demand, manufacturers can test different production plans virtually. This allows them to identify bottlenecks, optimize resource allocation, and create highly efficient schedules. Consider an automotive manufacturer using a digital twin to simulate the assembly line.
They could test different sequencing of tasks, robot placement, and worker assignments to identify and eliminate potential slowdowns, ultimately resulting in faster production and reduced lead times. The ability to test various scenarios before implementation allows for fine-tuning of production processes for maximum speed and efficiency.
Digital twins are revolutionizing manufacturing, offering unprecedented efficiency gains through virtual testing and optimization. It’s a stark contrast to the wasteful practices highlighted in this article about how Brazilian lawmakers won extra powers to waste money: how brazilian lawmakers won extra powers to waste money. Hopefully, the transparency and efficiency offered by digital twins can help prevent similar situations in other sectors and promote responsible resource allocation.
Case Studies
Let’s dive into some real-world examples demonstrating the power of digital twins in accelerating manufacturing processes. These case studies highlight the diverse applications and impressive results achieved across various industries. We’ll examine the challenges faced, the solutions implemented using digital twins, and the quantifiable improvements in speed and efficiency.
Digital Twin Implementation in Automotive Manufacturing: Reducing Production Time for a New Engine
A major automotive manufacturer used a digital twin to simulate and optimize the production line for a new engine design. The physical prototyping and testing process was significantly time-consuming and expensive. By creating a digital twin of the entire assembly line, engineers could virtually test different layouts, identify bottlenecks, and optimize the workflow before any physical changes were made.
This virtual testing identified several areas where the production process could be streamlined, resulting in a 15% reduction in overall production time and a 10% decrease in manufacturing costs. The digital twin also allowed for the proactive identification and mitigation of potential assembly errors, minimizing downtime due to production line issues. The challenge was transitioning from a traditional, heavily reliant-on-physical-prototyping approach to a more data-driven, digitally-focused methodology.
The digital twin overcame this by providing a safe and cost-effective environment to experiment and iterate on the production process.
Improving Semiconductor Manufacturing Yield with Digital Twins: A Case Study in Precision
In the highly sensitive semiconductor industry, even minor variations in the manufacturing process can lead to significant yield losses. One leading semiconductor manufacturer implemented a digital twin to model its wafer fabrication process. This digital representation incorporated real-time data from sensors throughout the factory, allowing for continuous monitoring and analysis of the process parameters. The digital twin identified subtle variations in temperature and pressure that were previously undetectable, leading to adjustments in the manufacturing process.
The result was a 5% increase in yield, translating to significant cost savings and a faster production cycle. The challenge was the immense complexity of the semiconductor manufacturing process and the vast amount of data involved. The digital twin addressed this by providing a simplified, yet comprehensive, representation of the process, enabling effective analysis and optimization.
Digital twins are revolutionizing manufacturing, offering unprecedented efficiency gains through virtual prototyping and predictive maintenance. But rapid technological advancements also highlight the need for robust regulatory frameworks, as discussed in this insightful article on how to protect India’s shareholder capitalism from itself , to ensure responsible innovation and prevent potential exploitation. Ultimately, the ethical considerations surrounding such powerful tools are as crucial as the technological advancements themselves, impacting how we leverage digital twins for future manufacturing processes.
Optimizing a Pharmaceutical Production Line: Enhancing Efficiency and Reducing Waste
A pharmaceutical company used a digital twin to optimize its production line for a new drug. The company faced challenges related to complex regulatory requirements and the need to maintain stringent quality control standards. The digital twin allowed them to simulate various scenarios, including equipment failures and material shortages, enabling them to develop robust contingency plans. This resulted in a 12% reduction in production time and a 7% decrease in material waste.
Furthermore, the digital twin facilitated compliance with regulatory requirements by providing a comprehensive record of the manufacturing process. The challenge here was balancing the need for speed and efficiency with the stringent quality and regulatory requirements of the pharmaceutical industry. The digital twin overcame this by providing a virtual environment for testing and optimization while maintaining a detailed and auditable record of all manufacturing processes.
Comparative Analysis of Case Study Outcomes
Case Study | Industry | Production Time Reduction | Cost Savings |
---|---|---|---|
Automotive Engine Production | Automotive | 15% | 10% |
Semiconductor Wafer Fabrication | Semiconductor | (Indirect – Improved Yield) | (Indirect – 5% Yield Increase) |
Pharmaceutical Drug Production | Pharmaceutical | 12% | 7% |
Technological Aspects of Digital Twin Implementation
Building a successful digital twin in manufacturing requires a sophisticated interplay of various technologies. It’s not just about creating a virtual replica; it’s about creating a dynamic, responsive system that accurately reflects the real-world counterpart and allows for predictive and prescriptive actions. This requires a robust technological foundation capable of handling vast amounts of data and complex simulations.
The core technologies involved span data acquisition, processing, analysis, and visualization. Effective integration and interoperability between these technologies are paramount for a functional and reliable digital twin. Security considerations are also crucial, given the sensitive nature of the data involved.
Essential Technologies
Several key technologies are fundamental to creating and maintaining a functional digital twin. These technologies work together to capture, process, and analyze data, enabling the digital twin to accurately reflect and predict the behavior of its physical counterpart.
- Internet of Things (IoT) Sensors: These sensors are the eyes and ears of the digital twin, collecting real-time data from the physical asset. Data points such as temperature, pressure, vibration, and power consumption are continuously streamed to the digital twin platform. The density and type of sensors deployed depend heavily on the specific manufacturing process and the desired level of detail in the digital twin.
- Data Analytics: Raw data from IoT sensors is meaningless without analysis. Sophisticated data analytics techniques, including statistical analysis, time series analysis, and machine learning, are used to identify patterns, trends, and anomalies in the data. This processed information is then used to update the digital twin’s model and provide insights into the physical asset’s performance.
- Artificial Intelligence (AI) and Machine Learning (ML): AI and ML algorithms play a crucial role in predictive maintenance, process optimization, and anomaly detection. ML models can be trained on historical data to predict potential failures, optimize parameters for improved efficiency, and detect deviations from normal operating conditions, allowing for proactive interventions.
- Simulation Software: Sophisticated simulation software is used to model the physical processes within the manufacturing environment. This allows for “what-if” scenarios to be explored, enabling optimization of the process without impacting the physical production line. These simulations can range from simple models to complex physics-based simulations, depending on the complexity of the manufacturing process.
- High-Performance Computing (HPC): Digital twins, especially those representing complex manufacturing processes, generate and process vast amounts of data. HPC resources are often necessary to handle the computational demands of data analysis, simulation, and model updates in a timely manner.
Data Integration and Interoperability
Effective data integration and interoperability are crucial for a successful digital twin implementation. Data from various sources—IoT sensors, ERP systems, PLCs, and CAD models—must be seamlessly integrated to create a holistic view of the manufacturing process. This requires establishing standardized data formats and communication protocols.
Lack of interoperability can lead to data silos and hinder the digital twin’s ability to provide accurate and timely insights. Adopting industry standards such as OPC UA (Open Platform Communications Unified Architecture) can significantly improve data integration and interoperability.
Security Considerations
Security is a paramount concern in digital twin environments, given the sensitive nature of the data being collected and processed. Robust security measures are needed to protect against unauthorized access, data breaches, and cyberattacks. This includes implementing strong authentication and authorization mechanisms, data encryption, and intrusion detection systems.
Regular security audits and penetration testing are essential to identify and address vulnerabilities. A comprehensive security strategy should encompass all aspects of the digital twin architecture, from data acquisition to data storage and processing.
Designing a Digital Twin for Injection Molding
Let’s consider designing a digital twin for an injection molding process. The process involves several stages: material feeding, melting, injection, cooling, and ejection. A comprehensive digital twin would incorporate sensors at each stage to monitor critical parameters like temperature, pressure, and flow rate.
Data from these sensors would be integrated with CAD models of the mold and the machine, along with historical production data. AI/ML algorithms could then be used to predict potential issues like mold wear, material degradation, or process variations. The digital twin could simulate different scenarios (e.g., changing injection pressure) to optimize the process and minimize defects.
The design would also incorporate a user interface for visualizing the data and interacting with the digital twin. This interface would provide real-time monitoring of the process, predictive alerts, and recommendations for process adjustments. Robust security measures, including data encryption and access control, would be implemented throughout the system.
Future Trends and Challenges
The rapid advancement of digital twin technology is transforming manufacturing, but its full potential hinges on addressing emerging trends and overcoming significant hurdles. The next few years will be crucial in determining how seamlessly digital twins integrate into the manufacturing landscape, impacting everything from production efficiency to sustainability.The successful integration of digital twins across various manufacturing sectors depends on several factors, including technological advancements, overcoming implementation challenges, and fostering a skilled workforce.
Failure to address these factors could stifle the widespread adoption of this transformative technology.
Emerging Technologies Enhancing Digital Twin Capabilities
Several emerging technologies are poised to significantly enhance the capabilities of digital twins in manufacturing. These advancements will lead to more accurate, predictive, and versatile digital representations of physical assets and processes. Specifically, the convergence of artificial intelligence (AI), machine learning (ML), and the Internet of Things (IoT) will play a pivotal role. AI and ML will enable digital twins to analyze vast datasets, identify patterns, predict failures, and optimize processes autonomously.
The seamless integration of IoT devices will provide real-time data streams, enhancing the accuracy and responsiveness of digital twins. Furthermore, advancements in high-fidelity simulation and advanced sensor technologies will allow for more realistic and detailed representations of physical systems. For instance, the use of augmented reality (AR) and virtual reality (VR) will allow engineers to interact with digital twins in more intuitive ways, facilitating design improvements and problem-solving.
Challenges Associated with Widespread Adoption
Despite the immense potential, several challenges hinder the widespread adoption of digital twin technology. High initial investment costs, including the expense of hardware, software, and skilled personnel, can be a significant barrier for many manufacturers, particularly small and medium-sized enterprises (SMEs). Data security and privacy concerns are also paramount. The integration of various data sources from different systems can be complex and time-consuming, requiring robust data management strategies.
Moreover, the lack of standardized protocols and interoperability issues can complicate the integration of digital twins into existing manufacturing infrastructure. Finally, the need for significant changes in organizational structure and workflows to effectively utilize digital twin data and insights represents a considerable challenge. For example, a manufacturer might struggle to integrate data from legacy systems with newer IoT-enabled equipment, creating inconsistencies and hindering the accuracy of the digital twin.
Skilled Workforce Development
The successful implementation and utilization of digital twins require a skilled workforce capable of designing, building, managing, and interpreting data from these complex systems. This necessitates a significant investment in education and training programs focusing on data science, AI, ML, simulation, and digital twin-specific expertise. The skills gap in these areas is already a significant concern, and proactive measures are needed to bridge this gap.
This includes collaborations between educational institutions, industry, and government to develop curriculum and training programs aligned with industry needs. Upskilling existing manufacturing personnel and attracting new talent through competitive salaries and career development opportunities are crucial for sustaining the growth of digital twin implementation. For instance, a manufacturing company might sponsor employees to pursue advanced degrees in data science or offer internal training programs on digital twin technologies.
Predicted Evolution of Digital Twins in Manufacturing (Visual Description)
Imagine a timeline stretching over the next five years. At the beginning (Year 0), digital twins are primarily used for isolated processes, represented as simple 2D models with limited data integration. By Year 2, the digital twins become more sophisticated, incorporating 3D models with improved data integration and basic predictive capabilities. These are represented by a richer, more detailed model with data streams visualized as flowing into it.
Year 3 shows the emergence of AI-powered digital twins, depicted by intelligent algorithms overlayed on the 3D model, highlighting predictive analytics and autonomous optimization. By Year 4, the digital twins are fully integrated into the manufacturing ecosystem, forming interconnected networks visualized as a web of interconnected digital twins, each representing a different aspect of the manufacturing process. Finally, in Year 5, the digital twins are highly personalized and adaptable, with customizable interfaces and advanced AR/VR integration represented by a highly interactive and immersive representation of the manufacturing process, allowing for real-time collaboration and decision-making.
This evolution showcases a transition from simple, isolated models to complex, interconnected systems with advanced AI capabilities and user-friendly interfaces.
The impact of digital twins on manufacturing speed is undeniable. By providing a virtual playground for experimentation and optimization, they’re not just improving efficiency – they’re fundamentally changing how we approach manufacturing. From reducing costly downtime to accelerating innovation, the potential is vast, and as the technology matures, we can only expect even greater leaps forward in productivity and efficiency.
The future of manufacturing is digital, and it’s faster than ever before.